The Benefits and Advantages of Low Pressure Casting in Modern Business
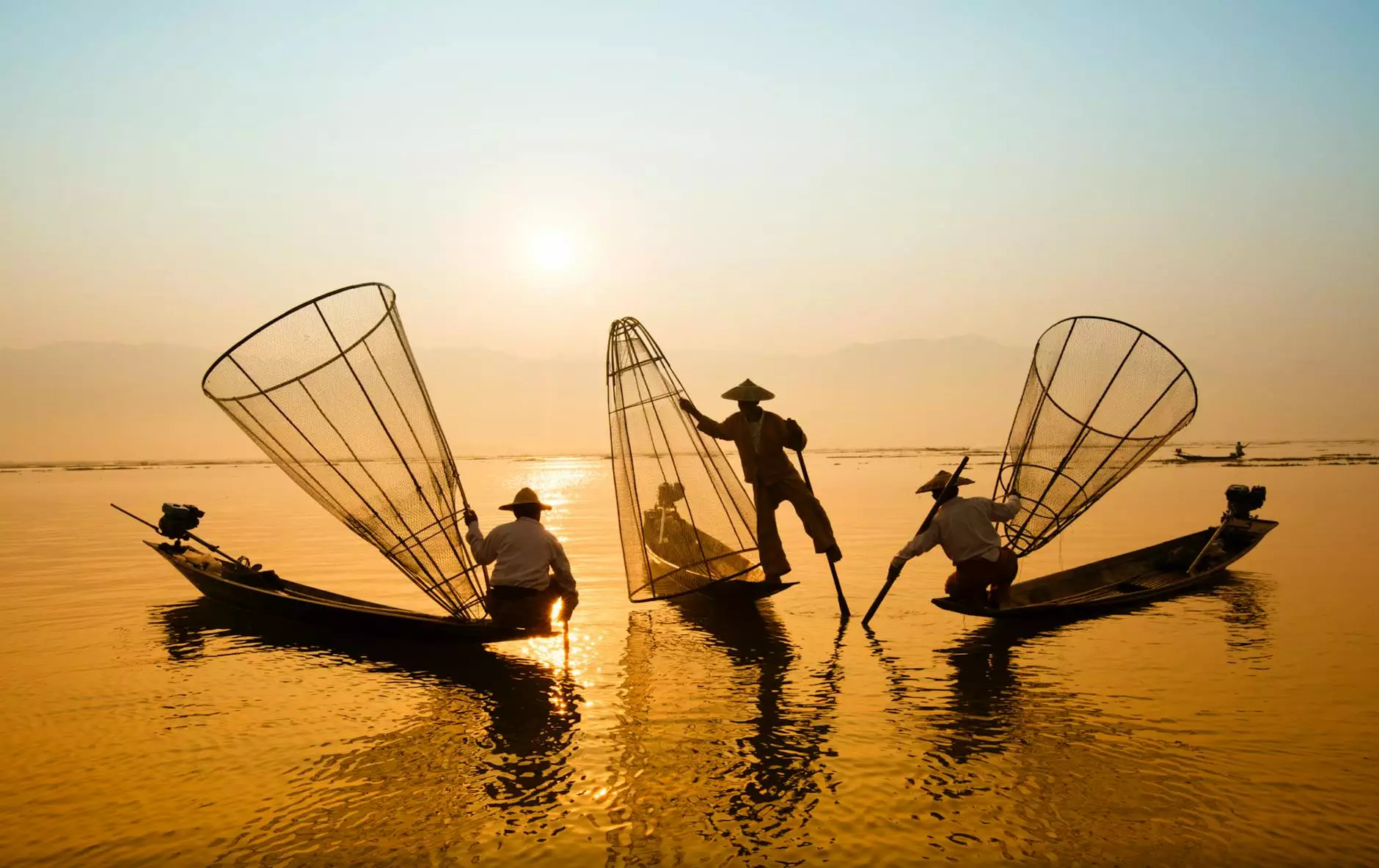
In the ever-evolving landscape of manufacturing and product design, low pressure casting has emerged as a vital process that brings numerous advantages to businesses across various industries. This article delves deep into the world of low pressure casting, exploring its uses, benefits, and significance within the realms of art supplies, product design, and 3D printing. Understanding this innovative manufacturing technique can empower businesses, enabling higher quality output while optimizing costs and time.
Understanding Low Pressure Casting
Low pressure casting is a manufacturing process where molten metal is poured into a mold under low pressure. Unlike traditional casting methods, which rely on gravity or vacuum, low pressure casting utilizes controlled pressure to ensure that the metal fills the cavity evenly and completely. This precise method results in superior quality castings with enhanced mechanical properties and fewer defects.
The Process of Low Pressure Casting
The low pressure casting process involves several key steps:
- Molding: The process starts with the creation of a mold, typically made from high-quality materials capable of withstanding thermal stress.
- Melting: The metal chosen for casting is melted in a furnace until it reaches a liquid state. Common metals include aluminum, magnesium, and zinc.
- Pressurization: Once the metal is molten, it is transferred to the mold, where low pressure (generally between 0.5 to 2 bar) is applied to facilitate the flow of metal into intricate mold designs.
- Curing: After the mold is filled, it is allowed to cool and solidify. The low pressure ensures that even the tiniest details in the mold are captured.
- Demolding: The final step involves carefully removing the casting from the mold, which may involve mechanical tools, depending on the complexity of the design.
Key Advantages of Low Pressure Casting
Adopting low pressure casting in your production processes can lead to a multitude of benefits:
1. Enhanced Quality of Castings
One of the primary reasons businesses choose low pressure casting is the increased quality of the final products. The technique allows for:
- Better surface finish: The low pressure method eliminates air pockets and allows for smoother surfaces.
- Dimensional accuracy: Castings produced through this method have tighter tolerances, reducing the need for further machining.
- Fewer defects: The controlled environment minimizes the occurrence of casting defects such as porosity and shrinkage, leading to higher yield rates.
2. Cost-Effective Manufacturing
For many businesses, profitability is key. Employing low pressure casting can significantly cut costs due to:
- Reduced material wastage: The efficiency of the low pressure system enables better utilization of metal, decreasing material costs.
- Shorter cycle times: The quick cooling and solidification lead to rapid production, enhancing throughput.
- Lower energy consumption: Compared to high-pressure casting methods, the energy requirements for low pressure casting are generally lower.
3. Versatility Across Industries
Low pressure casting is not limited to one specific industry but is applicable to a variety of sectors, including:
- Automotive: Components such as engine parts and wheels are often produced using this method for their robustness and light weight.
- Aerospace: Precision and reliability are paramount in aerospace applications; hence, low pressure casting is preferred for creating critical parts.
- Art Supplies: In the art supply sector, low pressure casting can be utilized to create intricate tools and components that artists rely on.
- Product Design: Designers utilize this method to craft prototypes and final products due to its versatility and detail capabilities.
4. Environmentally Friendly Approach
In an era where sustainability is a priority, low pressure casting offers an environmentally friendly alternative. Some notable points include:
- Efficiency in resource use: The process maximizes material efficiency, leading to less waste.
- Lower emissions: Reduced energy consumption contributes to lower emissions and a smaller carbon footprint.
Applications of Low Pressure Casting in Various Industries
Understanding how low pressure casting is applied across industries can provide insights into its versatility and importance. Below are some specific applications:
1. Art Supplies Manufacturing
In the production of art supplies, low pressure casting offers distinct advantages. Tools such as sculpting aids or molds for casting can be created with intricate designs that resonate with artists’ needs. The process helps in achieving consistent quality, which is vital for both professional and amateur artists.
2. Product Design and Prototyping
For product designers, the ability to create high-fidelity prototypes rapidly is crucial. Low pressure casting allows designers to quickly transition from digital models to tangible products, facilitating faster iterations and refinements based on user feedback. This flexibility helps businesses respond swiftly to market demands.
3. Jewelry and Decorative Items
The jewelry industry has leveraged low pressure casting to produce detailed pieces and components with minimal waste. The capability to embed fine details results in high-quality artisan pieces that appeal to consumers seeking uniqueness and craftsmanship.
Investing in Low Pressure Casting Technology
Investing in the right technology is essential for businesses seeking to implement low pressure casting. Here are some considerations:
1. Choosing the Right Equipment
When selecting machinery for low pressure casting, it is critical to consider:
- Quality of the furnace: Ensuring the furnace can maintain precise temperatures and handle the required metal types.
- Mold design: Factory setups should have options for custom molds to accommodate specific designs.
- Automation capabilities: Advanced equipment can increase efficiency and reduce labor costs.
2. Employee Training
Training personnel is equally important. Employees must understand:
- Safety protocols: Given the risks associated with molten metal, proper training ensures a safer working environment.
- Operational functions: Knowledge of how to operate casting machinery efficiently will lead to better utilization of resources.
3. Continuous Improvement
Businesses should embrace a culture of continuous improvement when using low pressure casting. This may involve:
- Monitoring production quality: Regularly assessing the quality of castings to identify areas for improvement.
- Implementing new technologies: Staying updated with advancements in casting technology can lead to enhancements in efficiency and quality.
Conclusion
In summary, low pressure casting is a transformative process that significantly benefits modern business operations. From enhancing the quality of products to providing cost savings and supporting sustainable practices, the advantages are manifold. Industries ranging from art supplies to aerospace can harness the power of this innovative casting technique to improve their offerings and respond to market demands effectively.
For businesses interested in embracing low pressure casting, investing in the right technologies and training can pave the way for success. With the ability to produce high-quality, detailed, and cost-efficient products, adopting this method may well be the key to thriving in today’s competitive landscape.
Explore more about how low pressure casting can benefit your business at Arti90.com.