Understanding the Landscape of Plastic Injection Mold Manufacturers in China
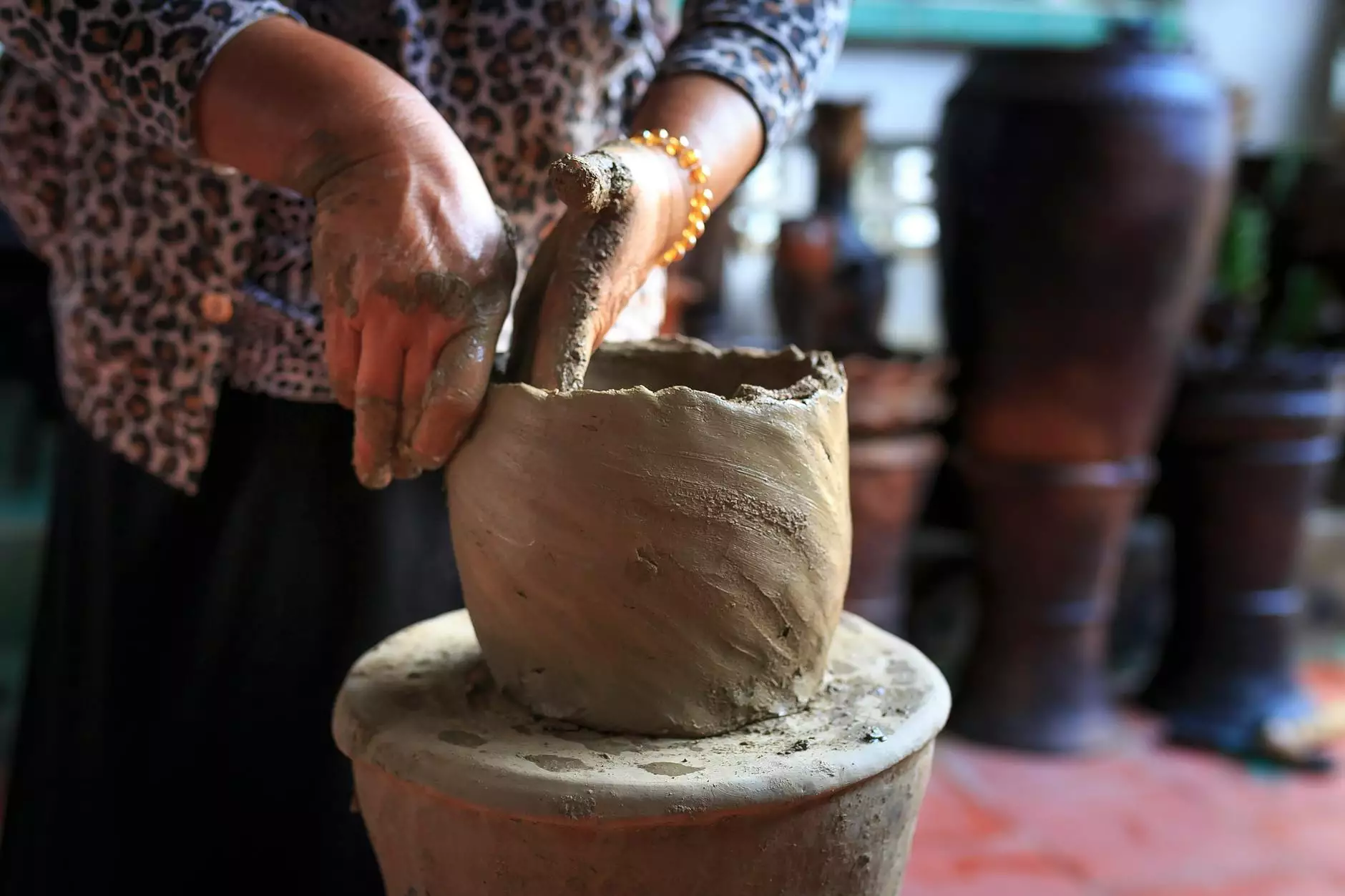
The booming manufacturing sector in China has positioned it as a global leader in the realm of plastic injection mold manufacturers. As industries evolve and the demand for innovative products increases, China stands out for its exceptional capabilities in plastic injection molding, providing manufacturers with high-quality molds at competitive prices.
The Significance of Plastic Injection Molding
Plastic injection molding is a pivotal process in manufacturing, allowing businesses to create parts and products with precision. This method is favored for several reasons:
- Efficiency: The process allows for large volumes of production, making it cost-effective for high-demand products.
- Design Versatility: Manufacturers can produce complex shapes and intricate designs that are often not feasible with other methods.
- Material Variety: A wide range of materials can be used, providing flexibility to meet specific product requirements.
- Quality Consistency: High precision and quality control ensure products remain consistent and meet stringent standards.
Key Advantages of Choosing Chinese Plastic Injection Mold Manufacturers
When looking to invest in plastic injection molds, China offers unparalleled benefits. Here are the key advantages:
1. Cost Efficiency
The cost of labor and materials in China is relatively low compared to Western countries. This means that plastic injection mold manufacturers in China can produce high-quality molds at a fraction of the cost, translating into significant savings for businesses.
2. Advanced Technology
Many Chinese manufacturers invest heavily in modern machinery and technology. This commitment ensures that they can produce molds with high precision and speed. Utilizing state-of-the-art CAD/CAM software and CNC machining enhances the quality of the molds manufactured.
3. Skilled Workforce
China's manufacturing sector benefits from a skilled workforce trained in the intricacies of plastic injection molding. The availability of engineers and technicians familiar with design and quality control procedures enhances the production process.
4. Short Lead Times
With streamlined processes and a robust supply chain, Chinese manufacturers can deliver plastic injection molds quickly. This is vital for businesses needing to bring their products to market swiftly.
5. Comprehensive Services
Many plastic injection mold manufacturers in China offer extensive services, including mold design, prototyping, and post-production support. This full-service approach ensures all aspects of the mold-making process are covered, facilitating a smoother experience for clients.
China’s Leading Plastic Injection Mold Manufacturers
With numerous options to choose from, identifying the right manufacturer can be daunting. Here are some notable players in the industry:
1. Hanking Mould
Hanking Mould is recognized for its commitment to quality and innovation. Specializing in both plastic mold making and manufacturing, Hanking Mould leverages advanced technology to create molds that meet the highest standards. Their extensive portfolio includes molds for various industries, ranging from automotive to consumer goods.
2. JG Mould
JG Mould focuses on precision and efficiency. With a specialization in complex mold designs, they cater to industries requiring intricate components. Their reputation for meeting tight deadlines while maintaining quality makes them a preferred choice among many global businesses.
3. Dongguan Dajun Mould
Dongguan Dajun Mould emphasizes customer service and overall satisfaction. With a team committed to understanding client needs, they provide tailored solutions in plastic injection molding. Their investment in state-of-the-art technology ensures they remain competitive in the industry.
The Plastic Injection Molding Process
Understanding the plastic injection molding process is crucial for businesses seeking to utilize this manufacturing method. The process typically involves the following steps:
1. Design and Prototyping
The first step involves creating a design blueprint for the product. Utilizing CAD software, manufacturers can produce a prototype to test functionality and fit. This step is vital for ensuring that the final product meets all specifications.
2. Mold Creation
Once the design is approved, the actual mold is created. This involves machining metal blocks that will form the mold cavities. Precision during this stage is crucial for achieving the desired product quality.
3. Injection
The mold is then subjected to the injection process, where molten plastic is injected into the mold under high pressure. This step allows the plastic to fill the mold and take its shape.
4. Cooling
After injection, the mold is cooled to solidify the plastic. This cooling phase is essential for achieving the required dimensions and strength of the finished product.
5. Ejection
Once cooled, the newly formed part is ejected from the mold. This must be done carefully to prevent any damage to the part or mold.
6. Finishing and Quality Control
The final stage includes any necessary finishing processes, such as trimming or surface treatment. Rigorous quality control measures ensure the final product meets all specifications and standards.
Challenges Faced by Plastic Injection Mold Manufacturers in China
While there are significant advantages, the industry also faces a few challenges:
- Intense Competition: With numerous manufacturers in the market, competition is fierce, potentially driving down prices and profit margins.
- Intellectual Property Concerns: Businesses must navigate potential risks associated with IP theft and ensure that their designs are protected.
- Quality Consistency: Maintaining consistent quality can be challenging, especially as demand fluctuates.
- Sustainability Pressures: Increasingly, manufacturers must address environmental concerns and adopt sustainable practices in their operations.
Future Trends in the Plastic Injection Molding Industry
As technology continues to advance, the future of plastic injection molding looks promising. Here are some emerging trends:
1. Automation and Smart Manufacturing
Automation is revolutionizing the manufacturing landscape. By integrating smart manufacturing technologies, manufacturers can enhance efficiency, reduce waste, and improve product quality.
2. Sustainable Practices
With growing environmental concerns, more manufacturers are seeking sustainable materials and processes. The use of recycled plastics and reduced energy consumption is becoming a priority.
3. Customization
Consumers increasingly demand customized products. Manufacturers are adapting by offering more tailored solutions while still leveraging the benefits of injection molding.
4. Advanced Material Use
The development of advanced materials, including bioplastics and composites, is expanding the possibilities of what can be achieved with plastic injection molding.
Conclusion
The world of plastic injection mold manufacturers in China is vast and continually evolving. With significant advantages such as cost efficiency, advanced technology, and a skilled workforce, China remains a dominant player in this sector. As businesses seek quality and efficiency in their manufacturing processes, understanding the capabilities and offerings of Chinese manufacturers becomes essential.
For those interested in exploring reliable and high-quality plastic injection molding solutions, Hanking Mould stands out as an industry leader, committed to excellence and innovation. Investing in a partnership with skilled manufacturers can lead to the successful development of products that meet market demands and exceed consumer expectations.
plastic injection mold manufacturers china