Maximizing Efficiency with Sticker Applicator: The Ultimate Guide
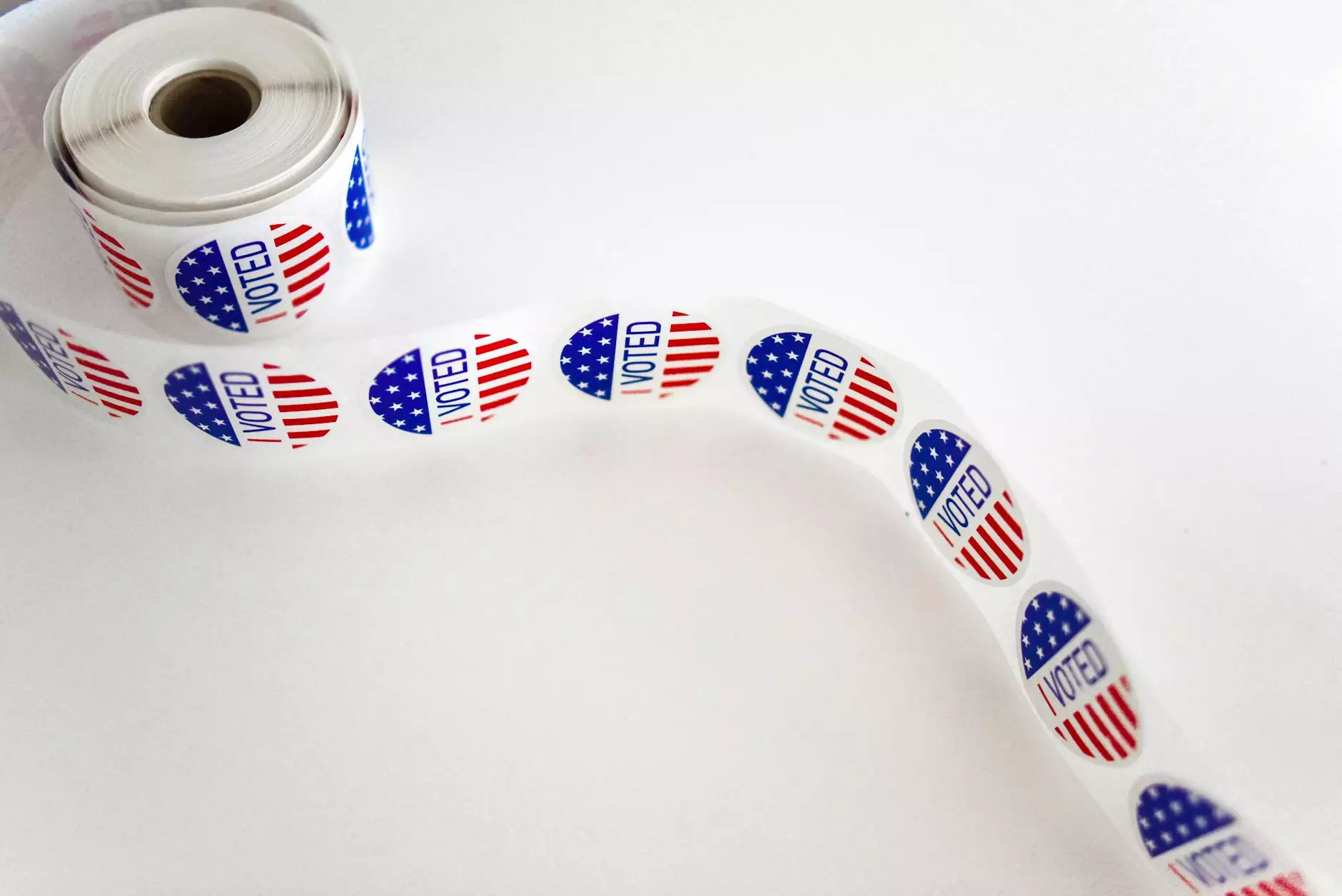
In the fast-paced world of business, where time is money and precision is key, the introduction of specialized tools can be a game-changer. One such innovation is the sticker applicator, a device that significantly streamlines the application of labels and stickers across various industries, including printing services, electronics, and computers. This comprehensive guide will delve into the world of sticker applicators, illustrating their importance, functionality, and the tremendous impact they hold for businesses aiming for efficiency and accuracy.
What is a Sticker Applicator?
A sticker applicator is a specialized device designed to automate the process of applying labels or stickers to products. It can be a simple hand-held tool or a sophisticated machine integrated into production lines. Typically used in manufacturing environments, these devices ensure that stickers are applied quickly and consistently, reducing labor costs and enhancing productivity.
The Importance of Sticker Applicators in Modern Business
As businesses continue to evolve and technology advances, the need for efficient labeling solutions has never been greater. Here’s why sticker applicators have become crucial in various sectors:
- Increased Efficiency: By automating the sticker application process, businesses can drastically cut down on the time required for labeling products.
- Consistency and Quality: Manual application can lead to errors or inconsistencies, while a sticker applicator ensures each label is applied uniformly.
- Cost Savings: Reducing labor costs and minimizing wasted materials directly impacts a company’s bottom line.
- Reduced Physical Strain: Automating handling tasks can lessen the risk of repetitive strain injuries among workers.
- Versatile Applications: Whether in the food industry, manufacturing or retail, sticker applicators can handle a range of products and surfaces.
How Sticker Applicators Work
Understanding the mechanics behind sticker applicators can help businesses choose the right tool for their needs. Here are the main components and processes involved:
1. Feeder Mechanism
The feeder mechanism is responsible for moving the stickers from their roll to the application area. This can be a simple gravity-fed system or a more complex servo-driven conveyor.
2. Applicator Head
The applicator head is the core of the operation, applying the sticker onto the intended surface. Depending on the model, it might use pneumatic pressure, a mechanical arm, or even a heated element for certain types of labels.
3. Sensor Technology
Modern sticker applicators often come equipped with sensors that detect the presence of products beneath the applicator, ensuring that no label is wasted and that each application is perfectly timed.
4. Control Interface
Most applicators feature a user-friendly control panel that allows operators to configure speed, alignment, and more, adapting the device to the specific needs of the production line.
Categories of Sticker Applicators
Not all sticker applicators are created equal. Depending on the scale of business operations and specific requirements, companies can choose from various categories:
1. Manual Sticker Applicators
Manual applicators are typically hand-held devices best suited for small-scale operations. They are cost-effective, easy to use, and provide a level of control that some operators prefer.
2. Semi-Automatic Sticker Applicators
These machines require some human intervention but automate the majority of the sticker application process. They are ideal for businesses that need to balance efficiency with budget constraints.
3. Fully Automatic Sticker Applicators
Designed for high-volume operations, these systems integrate seamlessly with production lines, applying stickers at exceptional speeds without the need for operator intervention.
Choosing the Right Sticker Applicator for Your Business
When selecting a sticker applicator, businesses should consider several factors to ensure they invest in the most appropriate technology:
1. Volume of Production
The expected number of products that require labeling will largely determine the type of applicator you need. High-volume operations will benefit from fully automated systems, while smaller businesses might start with manual options.
2. Type of Product
Different products require different labeling approaches. Consider whether your products are flat, cylindrical, or irregularly shaped, and choose an applicator that can handle these variations.
3. Label Specifications
Labels come in various sizes, materials, and adhesives. Ensure the applicator you select can accommodate the specific labels you plan to use.
4. Budget Constraints
While investing in a sticker applicator can save money in the long run, upfront costs can vary widely from one type to another. Prepare a budget that balances initial costs with potential savings in labor and materials.
Case Studies: Sticker Applicators in Action
To illustrate the effectiveness of sticker applicators, let's explore a few case studies from industries benefiting significantly from these tools:
Case Study 1: Food Packaging Industry
A leading food packaging company faced challenges in maintaining consistent labeling speed during peak production seasons. By integrating a high-speed fully automatic sticker applicator, they were able to increase production efficiency by 50%, reduce label waste by 30%, and enhance overall product presentation.
Case Study 2: Electronics Manufacturing
In electronics manufacturing, precision is key. A manufacturer of consumer electronics adopted a semi-automatic sticker applicator that allowed workers to apply labels uniformly, leading to a 40% reduction in labeling errors and a significant improvement in customer satisfaction.
Case Study 3: Cosmetic Industry
A burgeoning cosmetic brand struggled with high labor costs due to manual labeling processes. By investing in a manual sticker applicator for small batches, they reduced expenses and improved efficiency, allowing the brand to scale up production without additional labor costs.
Conclusion: The Future of Sticker Applicators
As the business landscape continues to evolve, the significance of automation and efficiency cannot be understated. The sticker applicator emerges not only as a simple tool but as a critical component in optimizing production processes across numerous sectors. With the advancement of technology, we can anticipate smarter, faster, and more versatile applicators that will further reshape how businesses operate.
Investing in a sticker applicator can transform your operational efficiency and help your business thrive in competitive markets like those represented by omegabrand.com. By making informed decisions and embracing automation, businesses stand to benefit greatly in both short-term productivity and long-term sustainability.
Ready to Transform Your Business?
Embrace the power of sticker applicators today. To learn more about how these tools can benefit your specific industry, contact us at omegabrand.com and take the first step towards operational excellence.