Exploring the Importance of Prototype Mould in Metal Fabrication
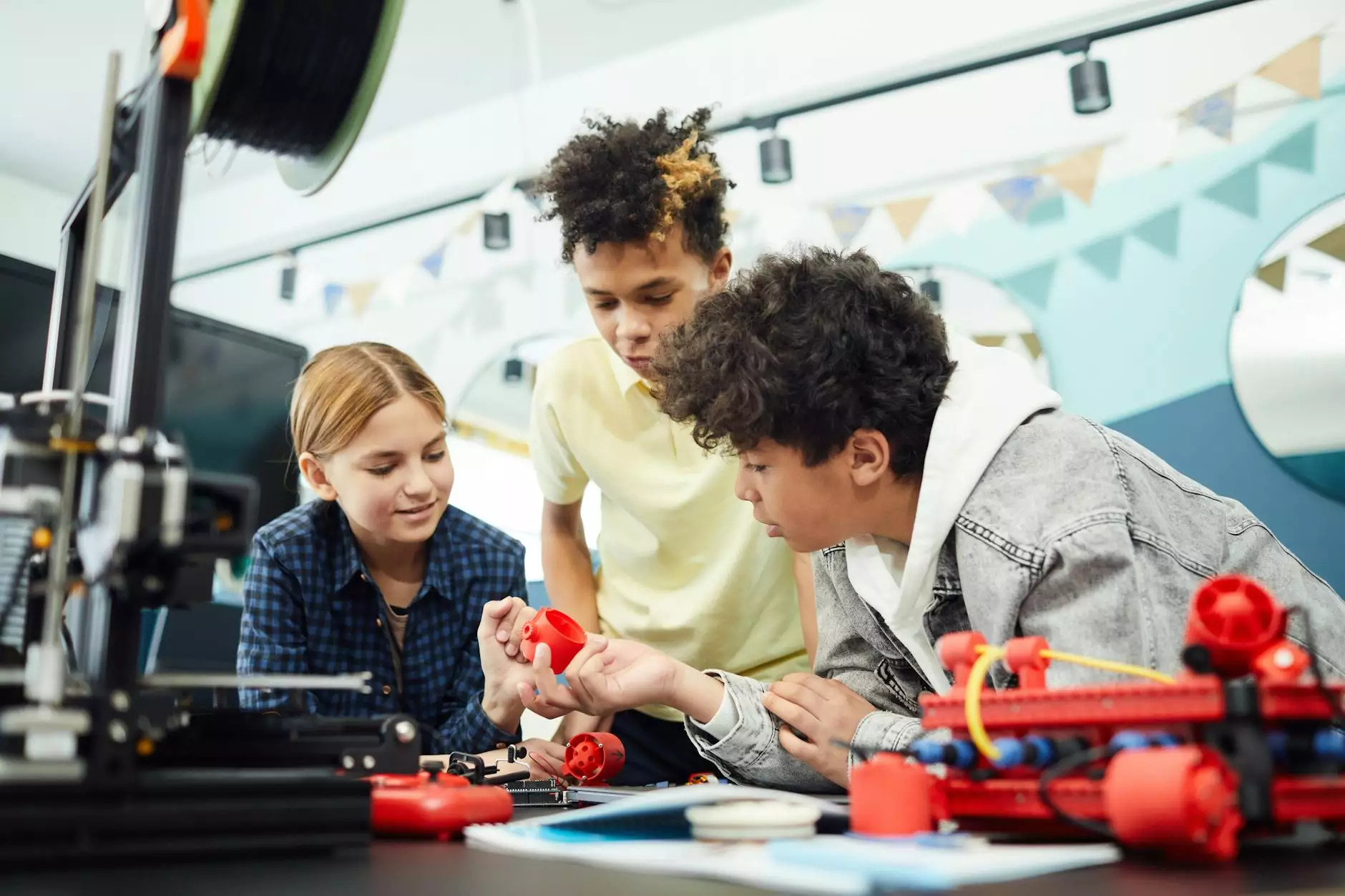
The evolution of the manufacturing industry is constantly driven by the need for precision, efficiency, and innovation. Within the domain of metal fabrication, one term that has gained significant traction is prototype mould. This article aims to unveil the importance of prototype moulds in metal fabrication and how they are crucial for developing high-quality products.
What is a Prototype Mould?
A prototype mould serves as a preliminary model or sample used in the manufacturing process. It is utilized to design, develop, and test new products before full-scale production. The prototype mould is essential for validating designs and ensuring that the final product meets the required specifications.
Why Are Prototype Moulds Important?
The significance of prototype moulds extends across various aspects of metal fabrication:
- Enhancing Design Accuracy: Prototype moulds enable designers to create accurate models of the final product. This leads to fewer errors during the production phase.
- Cost Efficiency: By identifying design flaws early in the process, businesses can avoid costly mistakes and reduce material waste.
- Speeding Up Time-To-Market: With rapid prototyping, companies can develop and test their products faster, allowing them to respond quickly to market demands.
- Facilitating Innovation: The ability to create physical prototypes encourages experimentation and innovation, leading to better quality products.
Types of Prototype Moulds in Metal Fabrication
There are various types of prototype moulds utilized in metal fabrication, each designed to fulfill specific requirements. Here are some of the most common types:
1. Injection Moulds
Injection moulds are widely used in the production of complex and high-volume plastic parts. They are designed to inject molten material into a mould, providing high precision and great flexibility in designs.
2. Die Casting Moulds
Die casting moulds are used for creating metal components. This method allows for the production of strong and lightweight parts with excellent surface finishes.
3. Blow Moulds
Blow moulds are mainly used in the production of hollow plastic parts such as bottles. This technique involves inflating hot plastic into a mould cavity to form the desired shape.
4. Compression Moulds
Compression moulds are utilized for creating thermosetting plastics. The process involves placing material into a heated mould which then cures to form a solid product.
The Process of Creating Prototype Moulds
Creating a prototype mould involves several critical steps, each of which plays a vital role in the overall quality and functionality of the final product:
1. Design and Conceptualization
The initial step involves the design of the product. This stage entails working with skilled designers who create detailed CAD (Computer-Aided Design) models of the product.
2. Material Selection
The choice of material is crucial in mould-making. Depending on the product specifications, different materials like aluminum, steel, or plastic may be selected based on durability, cost, and intended use.
3. Machining and Fabrication
Once the design is finalized and materials selected, the manufacturing process begins. Advanced CNC (Computer Numerical Control) machining is often employed to achieve high precision in mould construction.
4. Testing and Iteration
After the mould is manufactured, it undergoes rigorous testing. This stage involves creating several prototypes to evaluate functionality and performance. Feedback gained during this phase often leads to improvements.
Benefits of Using Prototype Moulds in Metal Fabricators
For metal fabricators like deepmould.net, implementing prototype moulds can yield numerous benefits:
- Increased Product Quality: Early testing ensures that the final product adheres to quality standards.
- Improved Customer Satisfaction: By providing prototypes for customer feedback, companies can ensure their products meet client expectations.
- Streamlined Production Processes: Eliminating design errors before mass production reduces the risk of delays and defects.
- Competitive Advantage: Rapid prototyping offers companies a chance to innovate faster than competitors, enhancing market presence.
Applications of Prototype Moulds
Prototype moulds have a wide array of applications across different industries:
Automotive Industry
In the automotive sector, prototype moulds are vital for developing components such as body panels, dashboards, and engine parts. The precise fit and functionality of these parts contribute to overall vehicle safety and performance.
Aerospace Industry
The aerospace industry relies heavily on prototype moulds for creating lightweight yet strong components. The rigorous testing and development phases ensure that every part meets strict safety and quality standards.
Consumer Electronics
In consumer electronics, the design and functionality of products are critical. Prototype moulds allow companies to refine the ergonomics and aesthetics of devices, ensuring a positive user experience.
Medical Devices
Prototype moulds are also used in the medical field, where precision and reliability are paramount. From surgical instruments to diagnostic devices, the prototypes need to conform to stringent health regulations.
Challenges and Solutions in Using Prototype Moulds
While prototype moulds provide numerous benefits, there are challenges that fabricators may encounter:
1. Initial Investment
The cost of developing prototype moulds can be substantial, especially for small businesses. However, investing in high-quality prototyping can lead to greater savings in production costs in the long run.
2. Time Constraints
The prototyping process can be time-consuming. Implementing project management software and agile methodologies can help streamline the process and reduce timelines.
3. Skill Gaps
The lack of skilled labor in operating complex machinery and software can hinder the prototyping process. Investing in training and development can enhance workforce capabilities.
The Future of Prototype Mould in Metal Fabrication
As technology advances, the future of prototype mould is poised for significant innovations. Emerging trends such as additive manufacturing (3D printing) and advanced materials are beginning to transform traditional mould-making processes. Companies that stay ahead of these trends will likely lead the charge in the highly competitive field of metal fabrication.
Conclusion
In conclusion, the role of prototype moulds in the metal fabrication industry cannot be overstated. They are essential for ensuring product quality, reducing costs, and expediting the product development cycle. As businesses strive for greater efficiency and innovation, embracing the power of prototype moulds will be vital for success.
By understanding the intricacies and advantages of prototype moulds, companies like deepmould.net can leverage these tools to enhance their product offerings and maintain competitive edge in the dynamic market of metal fabrication.