The Rise of Prefabricated Buildings: A Smart Investment for the Future
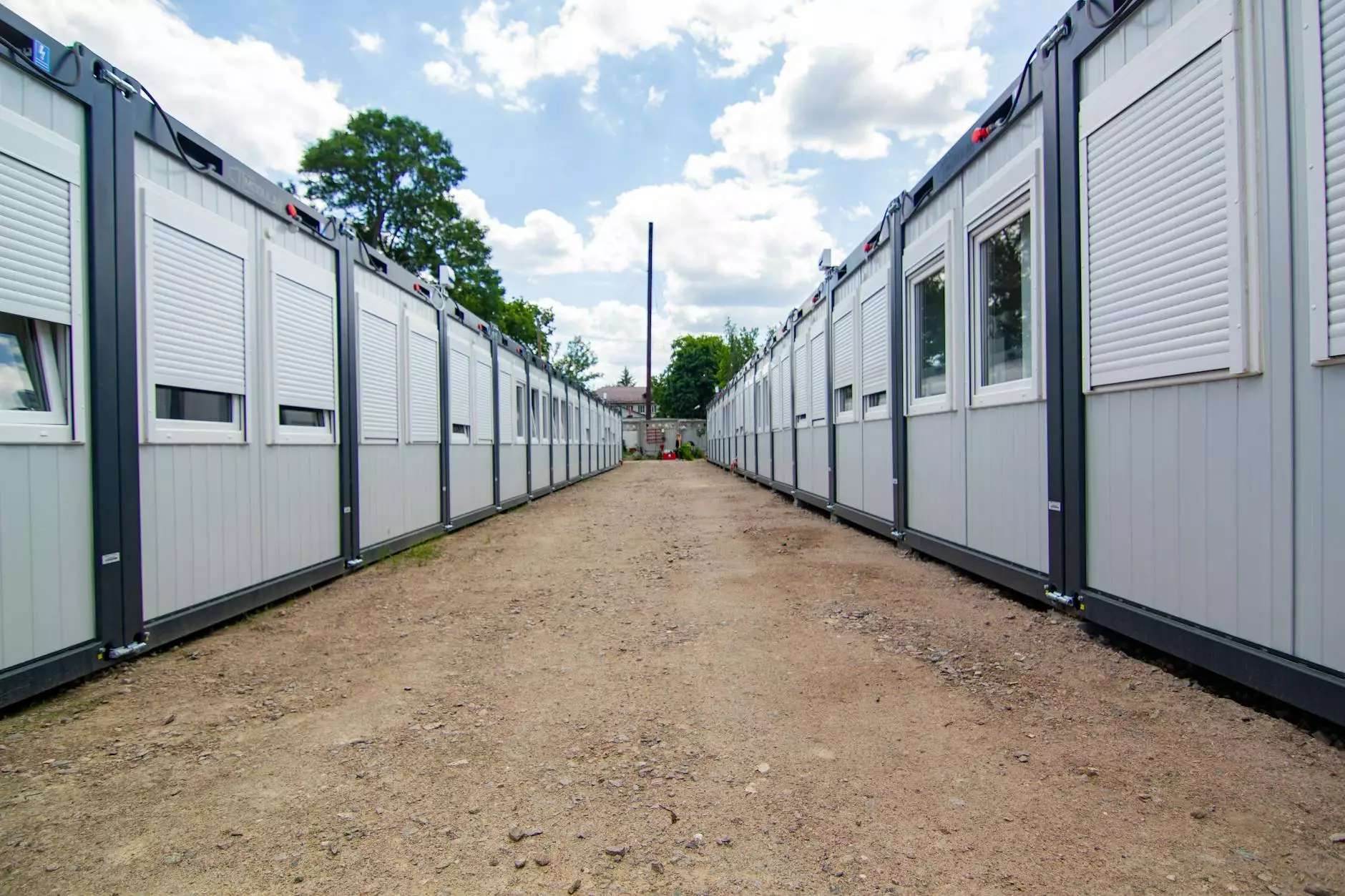
Prefabricated buildings are revolutionizing the construction industry, creating a paradigm shift in how we think about architecture, engineering, and sustainability. As more businesses and homeowners seek efficient solutions to building needs, prefabricated structures have emerged as a prominent option. In this comprehensive guide, we will delve deeply into prefabricated buildings, examining their benefits, construction process, and the factors that make them a smart investment for the future.
Understanding Prefabricated Buildings
Prefabricated buildings are structures that are manufactured off-site in controlled environments and then transported to their intended location for assembly. This method contrasts with traditional construction, where everything is built on-site, often leading to delays and inefficiencies. Prefabricated buildings can include anything from homes and schools to commercial structures and industrial facilities.
The Advantages of Prefabricated Buildings
There are numerous benefits associated with the adoption of prefabricated buildings:
- Time Efficiency: One of the most significant advantages of prefabricated construction is the reduced build time. Since components are produced simultaneously with site preparation, projects can be completed rapidly.
- Cost Savings: The efficiency of prefabrication often results in lower labor costs and minimized material waste, leading to overall cost savings.
- Quality Control: Off-site manufacturing in a controlled environment allows for better quality assurance and consistency compared to traditional methods.
- Sustainability: Many prefabricated buildings are designed with eco-friendly materials and practices, reducing their carbon footprint.
- Design Flexibility: Modern prefabricated buildings offer a wide range of customizable designs, adapting to various architectural styles and requirements.
Key Components of Prefabricated Building Construction
The construction of a prefabricated building involves several vital components, each contributing to the overall efficiency and effectiveness of the process:
1. Design and Planning
The initial phase in prefabricated construction is the design and planning stage. Here, architects and engineers collaborate to create a blueprint that meets both aesthetics and functionality.
2. Fabrication
Once the design is finalized, the fabrication of building components begins. This process occurs in a factory setting, where modules are constructed using standardized materials and methods to ensure quality and durability.
3. Transportation
After fabrication, the components are carefully transported to the building site. Advanced logistics and planning are required to ensure that all materials arrive on schedule and in proper condition.
4. Assembly
At the site, prefabricated modules are assembled to create the final structure. This process is much faster than traditional construction as it involves less on-site labor.
Different Types of Prefabricated Buildings
Prefabricated buildings can be categorized into several types, each serving different purposes:
- Modular Buildings: These are constructed in sections or modules, which can be combined in various configurations to create a variety of building types.
- Panelized Systems: In this type, pre-cut panels such as wall sections, flooring, and roofs are manufactured and assembled on-site.
- Pre-Cast Concrete: This method involves pouring concrete into molds that are built in a factory, offering immense strength and durability.
- 3D-Printed Buildings: A growing trend in the prefabrication industry, where buildings are created layer by layer using 3D printing technology.
Market Trends and Future of Prefabricated Buildings
The prefabricated building industry is witnessing immense growth, driven by several market trends:
Sustainability Goals
With a growing focus on environmental responsibility, many businesses are seeking sustainable building solutions. Prefabricated buildings largely contribute to sustainability goals through reduced waste and energy efficiency.
Technological Advancements
Innovations in technology, including Building Information Modeling (BIM), are enhancing the design and construction processes of prefabricated buildings. These advancements allow for better planning, visualization, and reduced errors.
Urbanization and Demand for Housing
The surge in urbanization has created a critical demand for housing. Prefabricated buildings offer a viable solution to address this issue quickly and efficiently.
Challenges in the Prefabricated Building Industry
Despite their many benefits, prefabricated buildings face several challenges that stakeholders must navigate:
- Regulatory Hurdles: Different regions have varying regulations regarding construction, which can complicate the adoption of prefabricated methods.
- Public Perception: Some consumers may have misconceptions about the quality and durability of prefabricated buildings.
- Limited Skilled Labor: While prefabrication reduces on-site labor, there remains a need for skilled workers to fabricate components.
Conclusion: A Bright Future for Prefabricated Buildings
The future of the construction industry is leaning towards prefabricated buildings as they offer a smart, efficient, and sustainable alternative to traditional construction methods. As technology continues to evolve and urbanization continues to demand quick housing solutions, these structures will play an increasingly vital role.
At Module-T, we are committed to providing the best in building supplies and services to support the growing trend of prefabricated buildings. With our extensive knowledge and expertise in the field, we can guide you in making informed decisions that not only meet your needs but also contribute to a sustainable future.
Whether you're a contractor looking to incorporate prefabricated solutions or a homeowner interested in innovative building options, the opportunities are vast in the realm of prefabricated construction. Join the revolution and experience the benefits that come with it.